Tridon Australia cutting manufacturing energy costs
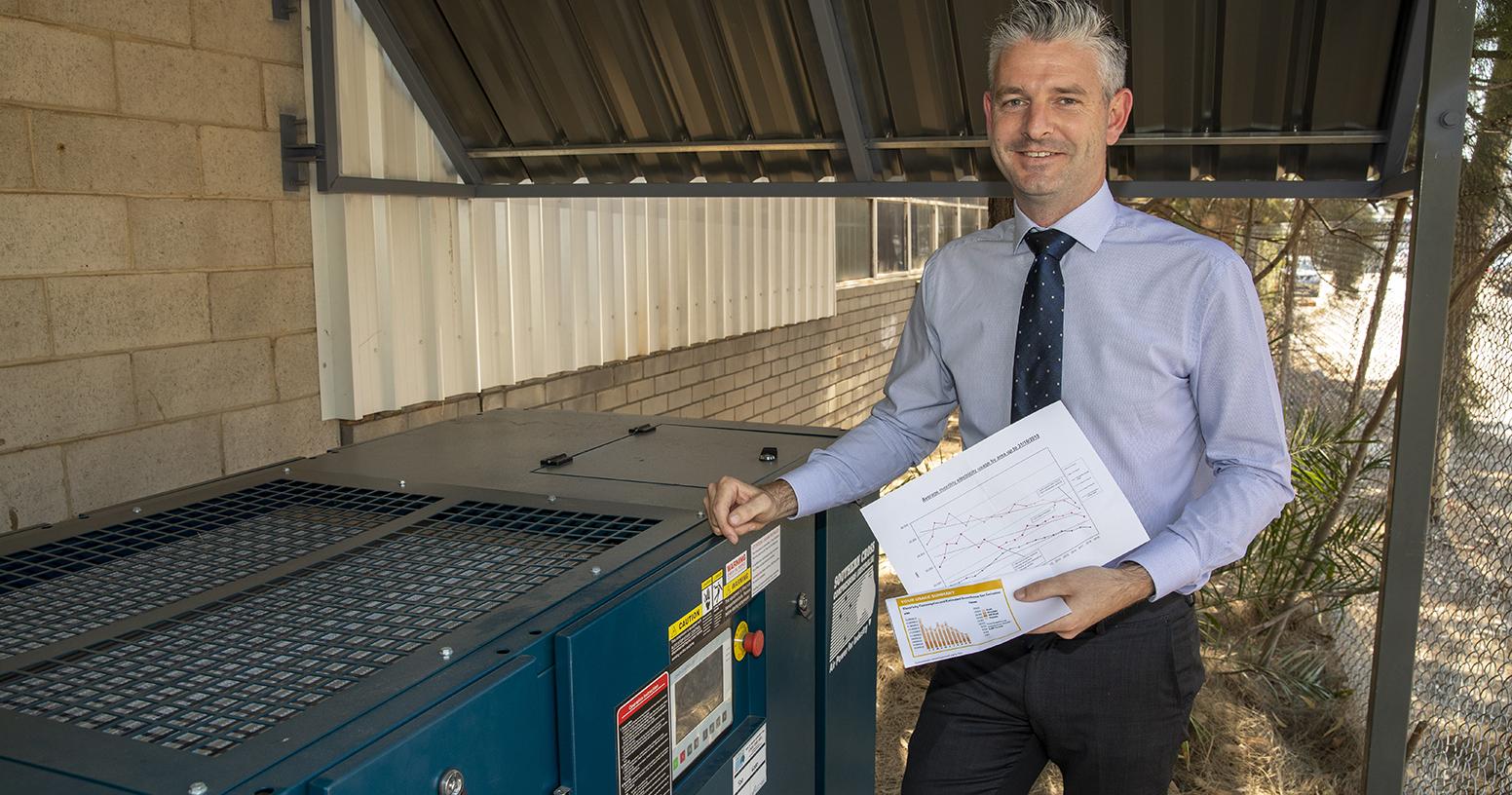
-
-
- About clean technology innovation
- CSIRO Data Clearing House
- Clean technology innovation grants
- Ecosystem grants FAQs
- Hysata’s electrolyser technology puts Australia at the forefront of the green energy revolution
- The Melt’s hardware accelerator and pilot enabler programs
- The product development lifecycle
- UoW Clean Energy Living Laboratory is set to be Australia's first mixed-use, precinct-based microgrid
- Business equipment upgrades
- Low emissions specifications
- NSW skills for net zero
- Industrial decarbonisation plans for the Hunter and Illawarra
-
- EV public charging master plan
-
- Destination charging grants FAQs
- Electric vehicle destinations charging grants: previous round information
- Eligible EV charger and software list
- Future proofing business: motel's EV success
- How hosting an EV charger can benefit your business
- How to make your town a preferred charging stop for EV drivers
- Mingara Recreation Club
- Net zero buildings
- Pumped hydro grants
-
-
-
- Find an energy course
-
- Battery storage guide
- Circular design guidelines for the built environment
- Compressed air guide
- Electricity metering and monitoring guide
- Energy efficient lighting guide
- Gas measurement and monitoring guide
- HVAC guide
- Industrial refrigeration guide
- Renewable energy guides for farmers
- Voltage optimisation guide
-
- NSW innovation that is wow
- Grant’s business got a head start with new energy efficient refrigerators
- AGL steering towards an electric future
- Advancing hydrogen storage technology
- An holistic approach to sustainability
- Collaboration is key to Port Authority’s prize-winning plan for net zero
- Driving sustainability: how STARTTS is transitioning to an EV fleet
- High impact partnership
- Second life solar
- Port of Newcastle fleet heading all electric
- Tridon Australia cutting manufacturing energy costs
Operations Manager Luke Rhodes was sitting in his office at Tridon Australia, a manufacturer and distributor of automotive parts, when he got an unusual email.
It was from the utility company asking if something was wrong at their Sydney factory – the energy bill in one building had dropped a staggering 65% in 4 weeks.
Instead of being worried, Rhodes and his colleagues were amused. “It was pretty funny,” he recalls. They were also pleased that their strategy to make their large industrial site more energy efficient had paid off.
Over the past year, Tridon Australia had been implementing a range of energy savings measures including LED lighting and solar panels. The massive drop in energy, however, was largely attributed to their new compressed air system, which the NSW government partially paid for.
Tridon is one of around 90 sites across NSW —nearly half of them in the regions— which have taken advantage of government funding which helps businesses be more energy efficient. Manufacturers have upgraded their boilers and refrigeration systems, installed new meters and looked into improving their processes.
For Tridon, their old compressed air system was the problem. Rhodes says it was pumping around 55 to 60 kilowatts while the rest of the facilities —air conditioning, heating, everything included— were around 18 to 20 kilowatts.
He says getting the government funding was easy and “serendipitous” as it happened just as they were assessing their compressed air system. The NSW government contributed $10,000 towards the project and Tridon pitched in $32,000. With the money they will save from their electricity bill dropping, Rhodes says they will break even in 2 years.
“I back the program 100% just for the sheer volume of money and energy you can save. It’s a no-brainer, really. I didn't anticipate that we’d get this much energy savings, so it's been fantastic.”